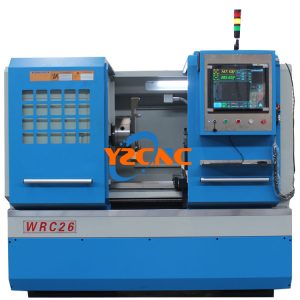
Menu
Standard Configuration :
Spindle speed:800rpm
Rotary table:500*500mm
Indexing accuracy:±3″
Repeatability:±1″
Certification: CE/SGS
Type: Horizontal
Warranty: 18 months
Voltage: As customers’ requirement (380V/400V/220V)
Color: As customers’ requirement
After-sale service: Overseas door-to-door installation and commissioning can be provided
A horizontal Cnc machining center (HMC) is a type of machine tool used in the manufacturing industry for precision metalworking. HMCs are designed to perform a wide range of operations, including milling, drilling, boring, tapping, and reaming, with high accuracy and efficiency. Compared to vertical machining centers (VMC), HMC have several advantages in terms of workpiece accessibility, chip evacuation, and stability. we will discuss the key features and benefits of HMCs, as well as their applications, types, and industry trends.
The HMC500 horizontal machining center has high rigidity and good machining accuracy. It adopts a 500×500mm worktable, which can automatically and continuously complete various processes such as milling, drilling, boring, expanding, and reaming of parts. It can be widely used in the machinery industry. And mechanical processing in other industries, especially for batch processing of small and medium box parts, mold processing and more precise parts processing has strong applicability.
Item | Unit | HMC500 | |
Processing range | X/Y/Z axis travel | mm | 700x600x580 |
Spindle center to table surface | mm | 90-690 | |
Spindle nose to table center | mm | 120-700 | |
Working table | Table size | mm | 500×500 |
Max. loading | kg | 400 | |
Min. Indexing angle | 1° x360 | ||
T slot size | mm | 5x18x80 | |
Main spindle | Spindle speed | rpm | 8000 |
Spindle taper | BT40-150 | ||
Main motor | 11/15 | ||
Others | Lead screw (X/Y/Z) | mm | X/Z: Φ40-16 Y: Φ40-12 |
Weight | kg | 6000 |
The basic components of horizontal cnc machining center(HMC) include a worktable, a spindle, an ATC (automatic tool changer), a coolant system, and a control unit. The worktable is typically a pallet or a rotary table that can hold multiple workpieces or fixtures. The spindle is a motor-driven shaft that rotates the cutting tool at high speeds and feeds it into the workpiece. The ATC is a mechanism that can automatically exchange the cutting tools as needed, reducing the setup time and increasing the production rate. The coolant system is used to lubricate and cool the cutting tool and the workpiece, preventing overheating and tool wear. The control unit is the brain of the machine, which receives the program instructions from the operator or the CAM (computer-aided manufacturing) system and executes them with precision.
One of the main advantages of Horizontal machining center (HMC )is their horizontal spindle orientation, which allows the workpiece to be loaded and unloaded from the front or the sides of the machine, instead of from the top as in Vertical cnc machining center ( VMC )This feature enables HMC to handle larger and heavier workpieces, as well as to perform multiple operations on different sides of the workpiece without repositioning it. Moreover, HMC can provide better chip evacuation and coolant flow, since the chips and fluids can fall freely away from the cutting zone, reducing the risk of chip clogging and tool breakage. In addition, HMC can offer higher stability and accuracy, especially in long and heavy cuts, as the workpiece is supported by the table and the spindle during the machining process.
The use of Horizontal machining center can bring many benefits to the manufacturing process, such as:
Higher productivity: HMC can reduce the cycle time and increase the output rate by performing multiple operations in one setup, eliminating the need for manual intervention, and minimizing the idle time between tool changes. Horizontal machining center (HMC ) can also provide faster and more consistent cutting speeds and feeds, resulting in higher material removal rates and surface finishes.
Lower costs: Horizontal machining center (HMC )can lower the labor and material costs by reducing the scrap rate, the tool consumption, and the tool changeover time. HMC can also save floor space and energy costs by consolidating multiple operations into one machine, reducing the need for auxiliary equipment and transportation.
Improved quality: HMCscan improve the dimensional accuracy, the geometric tolerances, and the surface integrity of the workpiece by reducing the vibration, the deflection, and the thermal distortion of the machine and the tool. HMC can also enhance the consistency and repeatability of the machining process by using the same tool paths and parameters for multiple workpieces.
HMC can be used in various industries and applications, such as:
Aerospace: HMCcan machine large and complex parts for aircraft and spacecraft, such as wings, fuselages, engine components, and landing gears. HMCs can also handle exotic materials, such as titanium, Inconel, and composites, with high precision and reliability.
Automotive: HMC can produce engine blocks
1. The main basic parts such as the base, the bed, the middle sliding seat, the worktable, and the spindle box are made of high-rigidity cast iron structure, and the inner cavity is distributed with network-like reinforcement ribs, which ensures the high rigidity and bending resistance of the basic parts. The shock performance; the base parts are molded with resin sand and subjected to aging treatment to ensure the stability and reliability of the long-term use accuracy of the machine tool.
2. The X, Y, and Z axes adopt Taiwan Shangyin linear guide rails, and adopt the span support method of two guide rails, with stable operation and stronger bearing capacity; the center of the workbench is always within the span when the movement limit is reached, which improves the The stability of the machine tool motion process improves the machining accuracy and surface quality of the product.
3. The feed in the three directions of X, Y, and Z adopts large-pitch, high-precision, high-strength ball screws, and the feed speed is high; the servo motor is directly connected to the lead screw with an elastic coupling, and the feed servo motor directly transmits power Provide high-precision ball screw to ensure the positioning accuracy of the machine tool.
4. The guide rails in the three directions of X, Y and Z are sealed and protected to ensure the cleanliness of the guide rails and ensure the transmission and motion accuracy of the machine tool.
5. The screw support adopts pre-stretching structure, which greatly reduces the influence of thermal deformation on the accuracy of the machine tool during long-term operation.
6. The Z-direction lift is equipped with a nitrogen balance system to improve the quality of the machine tool to achieve high-speed, high-precision processing and reduce the load of the servo motor to increase the life of the machine tool;
7. The spindle adopts a high-speed, high-precision, and high-rigidity spindle unit of a well-known Taiwanese brand, with strong axial and radial bearing capacity. The main shaft has an air curtain protection device, which completely avoids the penetration of cutting fluid and dust, ensures the accuracy of the main shaft and prolongs the service life;
8. Adopt high-quality 24 high-speed automatic tool changers from Taiwan, with accurate tool change, short time and high efficiency. After operation test, it meets the reliability requirements.
9. The machine tool adopts an advanced centralized automatic lubricating device, with regular and quantitative automatic intermittent lubrication, and the work is stable and reliable.
10. The machine tool is equipped with imported famous CNC control system, which has complete functions, easy operation, stable and reliable precision.
11. The electrical system adopts the separate design structure of the transformer and the control system to reduce heat generation, reduce the temperature change of the electrical box, and improve the service life of electrical components and the reliability of system control.
12. The operating system of the machine tool is designed according to the principle of ergonomics. The operation box is set independently, close to the operator. It is equipped with a hand-held electronic handwheel operation box, which is convenient for tool setting.